ARP 2000 Head Stud information
Do you have ARP2000 head studs in your VG engine? You may think you do but you likely do not if you bought them in the last 6 years or so from any Z specific vendors. There is a real good chance you actually have the weaker chromoly 8740 head studs and didn't even know it!
Did I peak your curiosity? Then please read this entire write up to learn all about this issue.
In our recent business ventures here at ZShack, we decided to open a Web Store and offer our community OEM & Performance parts options at a fair price with quality tech help and advice from Z32 experts.
In doing so we uncovered some information that most people are not aware of about ARP studs!
We have decided to educate the community about this issue as well as offer an authentic kit for those that want the real deal. We in no way imply that other vendors knowingly did anything wrong and we are not here to discuss their intentions nor create any shop to shop conflict etc. Our ONLY mission is to help this platform move forward in making more power than ever before. To do this, the community needs to be informed about things that can harm their builds as well as what parts are needed to help them. Unfortunately there are shops out there that will sell the community on anything they can make money on with only their self preservation in mind and not what a person realistically needs in order to achieve a certain power goal.
We have decided to educate the community about this issue as well as offer an authentic kit for those that want the real deal. We in no way imply that other vendors knowingly did anything wrong and we are not here to discuss their intentions nor create any shop to shop conflict etc. Our ONLY mission is to help this platform move forward in making more power than ever before. To do this, the community needs to be informed about things that can harm their builds as well as what parts are needed to help them. Unfortunately there are shops out there that will sell the community on anything they can make money on with only their self preservation in mind and not what a person realistically needs in order to achieve a certain power goal.
The following is everything you need to know about head studs.
For those that do not know the history of Head studs for the VG30DE/TT and the 300ZX, I will start there.
For the longest time ARP has made a head stud and main stud kit for the VG30DE/TT. The head stud kit is part #202-4308 and the main stud kit is part #102-5402. The main kit is only offered in Chromoly 8740 by ARP. We are proud to offer our ZShack ARP2000 main stud kit. We put together our own main stud kit and are the first to offer this kit! Here is the link for them.
For the record, ARP head studs are only offered in ARP2000 material by ARP in their 202-4308 head stud kit for the VG30DE/TT engine. ARP does not offer ANY other head stud kits for our engine! Any kits other than the part number listed above, have been pieced together by someone other than ARP!
ARP head stud kits have always come with washers that are smaller than OEM head bolt washers. This has been a well known problem with using head studs on the VG! The smaller washers can and often will, indent or dimple the head surface where the washer sits, due to the smaller washer diameter not spreading the clamping area out enough to carry the torque load. This is a problem as it will reduce the clamping force of the fastener and will often lead to a blown head gasket due to head lift.
The old solution to this issue is well known amongst the OG VG engine builders. We would take the OEM washers and install them with the smaller ARP washers on top and then the ARP nut. This would fix the dimple issue and spread the clamping surface out to an acceptable level. This is where I believe the issue started. Vendors wanted to offer a larger washer, but ARP will not modify their kit to include the proper washers. (We have tried to get them to change their kits to no avail). Vendors took it upon themselves to create their own stud kits that would include the proper sized washers. That is a good idea and a help to the community. This also allowed them to sell the kits at a significantly lower price while increasing profit margins.
Again, the studs they are all selling are NOT ARP2000 material! They are all Chromoly 8740! A much weaker stud that is not to ever be used as a head stud on a high power engine! Some would argue that the material is not as strong as the OEM head bolts. While I do not have a credible source to reference for the strength of the OEM bolts, I will opt out of further speculating on this. Either way when we feel the need to upgrade to a stud it is usually due to a need for more clamping force than the OEM bolts can do for higher HP/TQ levels. I have seen OEM head bolts hold good to about 800whp before letting go. We have seen the chromoly 8740 let go far sooner than that. Using Chromoly in these builds is just asking for head gasket failure or worse and is simply unacceptable!
These 8740 head stud part numbers are for a ford Cosworth engine. The TQ level that they are recommended for is only when used in the ford Cosworth application. This is due to the fact that the Cosworth block has more thread engagement compared to the VG. These are ARP engineer's words, not mine as I have no access to a Cosworth engine to compare them to. When you contact ARP and ask them what the TQ yield of this bolt is, they will look up the part number and tell you a higher number than what they would be on a VG. This is because the Cosworth has more thread engagement with these bolts compared to the engagement in the VG. Primarily due to the shorter stud used on each head. A studs TQ Yield threshold is determined by the material it is made from, the size of the fastener, thread pitch, as well as the amount of threads the stud has to engage inside the block. YOU CAN NOT APPLY A STUDS YIELD POINT FOR A FORD COSWORTH ENGINE TO THE 300ZX VG30DE/TT. The actual TTY threshold of the 8740 stud used in a VG30DE block is far less than the Cosworth. After the engineer looked at all the data, they determined that the fastener would roll the threads around 83 Foot pounds.
These 8740 head stud part numbers are for a ford Cosworth engine. The TQ level that they are recommended for is only when used in the ford Cosworth application. This is due to the fact that the Cosworth block has more thread engagement compared to the VG. These are ARP engineer's words, not mine as I have no access to a Cosworth engine to compare them to. When you contact ARP and ask them what the TQ yield of this bolt is, they will look up the part number and tell you a higher number than what they would be on a VG. This is because the Cosworth has more thread engagement with these bolts compared to the engagement in the VG. Primarily due to the shorter stud used on each head. A studs TQ Yield threshold is determined by the material it is made from, the size of the fastener, thread pitch, as well as the amount of threads the stud has to engage inside the block. YOU CAN NOT APPLY A STUDS YIELD POINT FOR A FORD COSWORTH ENGINE TO THE 300ZX VG30DE/TT. The actual TTY threshold of the 8740 stud used in a VG30DE block is far less than the Cosworth. After the engineer looked at all the data, they determined that the fastener would roll the threads around 83 Foot pounds.
If you go to the ARP catalog or call them on the phone, they will tell you that they will not sell the ARP2000 head studs in bulk in our head stud sizes. I think this is where the mistake was first made. Since the ARP2000 and the Chromoly 8740 look basically the same, they were probably thought to be the right fasteners for their kits! Perhaps this was a result of an overzealous parts manager looking to find a way to put a kit together with the right size washers while not having to toss out 16 smaller washers for every kit they sell. That is an added cost and a waste! So when these custom kits were put together, the person doing so either simply didn't know they were different or they just cared more about profit margin than performance of the fasteners. After all, back then we were not making the power we are these days with the VG and therefore most of your average VG builds would be fine on the Chromoly 8740 studs. But as we grow and make more power and the average VG power output threshold is increased, failure of the fasteners is inevitable! Don't be fooled, some vendors actually list the ARP 2000 part number (202-4308) on their website, but when you receive the parts, they will not be in the ARP packaging with that part number on the box. They will come in vacuum bags as seen in the pictures below!
The following image is of the part numbers that all z32 vendors are using in their head stud kits. If you look the part numbers up they will match up to the Chromoly 8740 part numbers and not ARP2000!

This next picture is to show the part numbers of the actual studs that are included with another vendor's kit. This is a part number for 8740.

The following picture is from Summit racing and is used since you cannot search ARP's website for information on bulk bolts. It shows the above stud part number is in fact a Chromoly 8740 part number! However I have personally called and spoke with ARP's Engineer/Tech and confirmed everything I am saying as true.

So how can you tell what head studs you have in your engine?
Here is how you can tell
Here is how you can tell
First off a real ARP2000 head stud kit will come in a box just like this

And not in a bag like this
The studs themselves are distinctively different as well.
The 8740 studs are a little longer, they are undercut and are marked with the words ARP ARP
Undercut means the shaft of the stud where there are no threads is made smaller.
The ARP2000 is on the bottom and the Chromoly 8740 is on the top.
As you can see here the real ARP2000's are marked ARP 2000 and the Chromoly 8740's are marked ARP ARP. We have confirmed with ARP engineers that all 8740's will be marked ARP twice, and the ARP 2000 will always be stamped as ARP 2000. So far I have checked the studs from every major Z specific vendor and they all are marked ARP, ARP indicating 8740.
Washers
As for the washer sizes, the following picture shows the size differences from regular ARP, to OEM and the larger size that should be used which we Include with our kits.
As you can see in these pictures, there is a significant difference between the 3 washers.
**When using our new larger washers, there is no need to double up on washers using the OEM washers as mentioned before. That is the old way of doing things!**
**When using our new larger washers, there is no need to double up on washers using the OEM washers as mentioned before. That is the old way of doing things!**
If you are interested in purchasing the real ARP2000 kit with the larger washers that you need, you can find them on our website or here
Proper head stud installation:
Another issue that can sometimes come up is the topic of stud installation.
Some people like to install the studs and back them out a couple of turns to "allow room for expansion due to heat" This is not a good idea for two main reasons. The first reason is that for every turn you back the stud out, the lower the amount of threads that are engaging the block from the stud. This will significantly reduce the fasteners strength and can lead to an over torque situation on the stud.
The second reason is that on a chromoly 8740 stud, like most have been using, the studs are longer than the ARP2000 studs. This combined with backing the stud out too far will lead to the nut tightening past the end of the threads and can cause a fastener failure under heavy loads due to a lack of thread engagement by the nut.
The second reason is that on a chromoly 8740 stud, like most have been using, the studs are longer than the ARP2000 studs. This combined with backing the stud out too far will lead to the nut tightening past the end of the threads and can cause a fastener failure under heavy loads due to a lack of thread engagement by the nut.
In this picture you can see how the nut can thread all the way past the studs threads and onto the undercut section of the stud. This cannot happen on the ARP2000 studs.
After taking some measurements of an undecked block and head (as seen in this picture), I found that the nut will run out of threads at a height from the head gasket surface of 66.5mm. At a height of 55.7mm the nut will fall completely off the stud. (The nut is roughly 11mm thick). So if you back a stud out too far you will lose threads for the nut to engage the stud in full due to the studs being longer than the actual ARP2000. You only have 11mm to play with and every turn you will lose thread engagement. You can clearly see this in the side by side picture of the studs above.
A stud's yield point is determined by the size of the stud and the amount of threads that the stud makes contact with in the block. So anytime you lose thread engagement, you lower the yield point of the fastener.
As per the engineer at ARP's recommendation, you should always clean up the threads in the block with a thread cleaner tool and clean the hole out very well. Then you will add ARP lube or regular engine oil to the threads on the block side of the stud. Never install a bolt/stud with dry threads!
You then want to fully insert the stud into the block and seat it down lightly but snug. In other words, make sure the stud goes fully in and is not stuck on a thread or debris. Then back the stud loose by just a hair to relieve tension.
Next use ARP lube on the washer, the threads on the upper part of the stud, the nut threads as well as the nuts washer face. Then follow the proper torque sequence/pattern and torque the heads in 3 equal steps. When you are using the torque wrench, you want to use a fluid motion and never start/stop while torquing. Going too slow will cause starting and stopping of the nut rotation and can cause false torque readings.
Now I know some of you are yelling at your screens right now saying, "Hey, what about using a better stud like an L19? Why all this talk about ARP2000's?"
Well, here is my answer to that. What I am about to say next has been discussed in great length with the engineers at ARP and they agree with and helped me come to my conclusions here.
If you are lifting a head with a true ARP2000 head stud then you have bigger issues than the hardware!
Well, here is my answer to that. What I am about to say next has been discussed in great length with the engineers at ARP and they agree with and helped me come to my conclusions here.
If you are lifting a head with a true ARP2000 head stud then you have bigger issues than the hardware!
That's right, I will say it again, If you are lifting a head with ARP2000 head studs that are properly installed and torqued to the correct specs then you have an issue with a tune etc. Not the studs!
Many other platforms use ARP2000 studs to roughly double the highest HP ever made with a VG! L19 is not a stud that is commonly used as a head stud in other platforms! Let's take GM's LS platform for example. They run ARP2000's well over 1500whp without any issue! In fact ARP does not sell any L19 Head Stud kits for the LS or the VG! The LS guys go from ARP2000's to Custom aged 625+ for the really big power builds.
I know where the trend for L19's started from and how they have been spread around the community as the new "go to" stud, but it is not a good choice to use them as a head stud.
I know you are thinking I am off my rocker, but as usual I have my reasons for what I am saying and the ARP engineer fully agrees with my next statements.
I know you are thinking I am off my rocker, but as usual I have my reasons for what I am saying and the ARP engineer fully agrees with my next statements.
L19 is a very brittle metal that is very susceptible to moisture. It is not to be touched by bare hands and must always be kept coated in oil. If not the fasteners can fail. Now let's consider what engines would be in need of a stud like the L19's?
Well it is the big power guys that need them. Since basically all the big power guys are running E85 to get those big power numbers, this is a bad combination. E85 is alcohol, and alcohol is a cold fuel that will introduce condensation in the engine block. Just ask anyone who has ran it and used a catch can. They will tell you their cans fill up with a stinky E85 water that they have to frequently empty. This condensation will end up making contact with the exposed threads on the head studs and can lead to premature failure of the stud.
*DISCLAIMER*
I will say that as of yet, to my knowledge, this has not happened, but it is not a risk worth taking.
Here is what the engineer at ARP said. The REAL ARP2000 studs can be torqued to a maximum of 125 ft lbs before reaching the studs yield. Since many VG builders are torquing the L19's to 120 FT/Lb's successfully, there is no reason an ARP2000 can't be torqued to the same level. The ARP 2000 yield strength, or the point in where the metal will stretch is 200,000 psi. L19 is 200,000 - 230,000 psi. Both will not reach yield until 125 Ft Lbs of torque or higher. The tensile strength or the point at which the bolt will break is higher on the L19, but both are still plenty high enough that if you ever broke one, it would be due to the engine operating out of an acceptable operating parameter! IE excessive head pressure or detonation etc.
The next best choice for a head stud would be ARP Custom Age 625+ which has a higher yield and tensile strength than L19 and can be torqued much higher than both ARP2000 and L19. But increasing torque on the head studs past 120 Ft Lbs is a problem for the heads anyway as the washer size is not sufficient enough to spread the load out to a point where the aluminum head won't cave in or crack. So a higher tensile strength stud would not really be much benefit to the VG. It would simply add a little more head room to the point where a stud would break. Which is already pretty high with ARP2000's. Since we can't torque higher without damaging the head surface under the washer, then we can't take full advantage of the better studs anyway right? Maybe in the future we will find a way to fit a larger washer in the head or a custom billet head will be designed with a larger surface in that area? So to summarize, You will get the same clamping force on both the ARP 2000 and the L19's, but the ARP2000 is not susceptible to moisture like the L19's are, which makes them a better option for cars running E85.
And again, ARP does not recommend the L19's to be used with E85!
Here is a description and a chart from the ARP catalog.


As you can see, they show using the L19 for rod bolts and not head studs. This is because a rod bolt will seal the threads into the rods when torqued and this will protect them from moisture. The engineer even said that they have seen boat engines recovered from underwater where the rod bolts had no rust/water damage because they were sealed. The same cannot be said for head/main studs. The picture above shows a statement where ARP says "This material is easily contaminated and subject to stress corrosion. It must be kept well-oiled and not exposed to moisture"
So for those of you that think you need or want a stronger fastener option, we are working on putting together an ARP Custom Age 625+ head and main stud kit. We now have an actual ARP 2000 main stud kit for the VG on our website available for purchase on our website www.zshackperformance.com
So for those of you that think you need or want a stronger fastener option, we are working on putting together an ARP Custom Age 625+ head and main stud kit. We now have an actual ARP 2000 main stud kit for the VG on our website available for purchase on our website www.zshackperformance.com
Our kit will come with both the original washers AND our larger washers. Again this is because ARP will not make the change to their kit. Even with us telling them about the issue!
So to summarize,
if you have a head stud that is stamped ARP, ARP then you have Chromoly 8740 studs. The kits that are being sold are recommending you torque the studs to 90 Ft Lbs. Some engine builders are on record stating they TQ them to 95 and higher. Be concerned, this is a problem as the 8740 studs will reach their yield at 83 Ft/Lbs. So if you torqued them to 90 as advertised, you have stretched the bolts past yield and have rolled or galled the threads on the studs. The studs should not be reused again for obvious reasons. If you look on ARP's website you will see they say to torque their head stud kit to 100 Ft. Lbs. This is a problem if you bought a 8740 kit and try torqueing them to what APR suggests. If you have the luxury that I have to be able to build so many VG's and use different types of fasteners, you would feel how the 8740's start to slip as you get to higher TQ levels. They will actually get tight, then snap and be looser. This is the threads galling or rolling over due to over torqueing them. When you TQ the real ARP 2000 studs, they go nice and tight without any slipping or snapping. The fastener feels smooth and intentional. Unlike the 8740 where you feel like something is breaking!
if you have a head stud that is stamped ARP, ARP then you have Chromoly 8740 studs. The kits that are being sold are recommending you torque the studs to 90 Ft Lbs. Some engine builders are on record stating they TQ them to 95 and higher. Be concerned, this is a problem as the 8740 studs will reach their yield at 83 Ft/Lbs. So if you torqued them to 90 as advertised, you have stretched the bolts past yield and have rolled or galled the threads on the studs. The studs should not be reused again for obvious reasons. If you look on ARP's website you will see they say to torque their head stud kit to 100 Ft. Lbs. This is a problem if you bought a 8740 kit and try torqueing them to what APR suggests. If you have the luxury that I have to be able to build so many VG's and use different types of fasteners, you would feel how the 8740's start to slip as you get to higher TQ levels. They will actually get tight, then snap and be looser. This is the threads galling or rolling over due to over torqueing them. When you TQ the real ARP 2000 studs, they go nice and tight without any slipping or snapping. The fastener feels smooth and intentional. Unlike the 8740 where you feel like something is breaking!
It is a real shame that these studs have been sold and used in so many engines now and that we are seeing an increase in blown head gaskets with them.
What is even more of a surprise to me is that with so many "experts" in our community, not one of them has discovered this issue before.......
Be careful who you trust your engine builds to, for things like this should be an eye opener for this community and a learning experience!
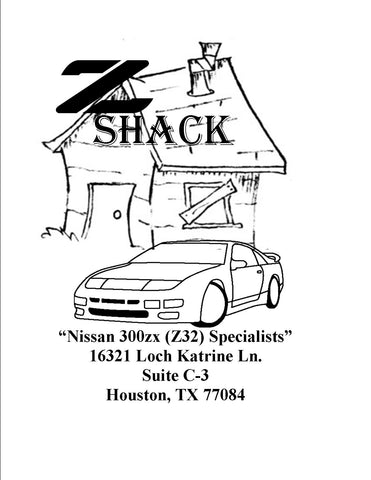
Written by:
Scott Taylor